Welding is the most widely used metal fabrication process. There are various categories of welding. Different operation requires separate welding techniques.
Stick welding and flux core welding has some things in common, but their working principle is distinct. In this discussion, we will see stick welding Vs flux core welding from a comparative point of view.
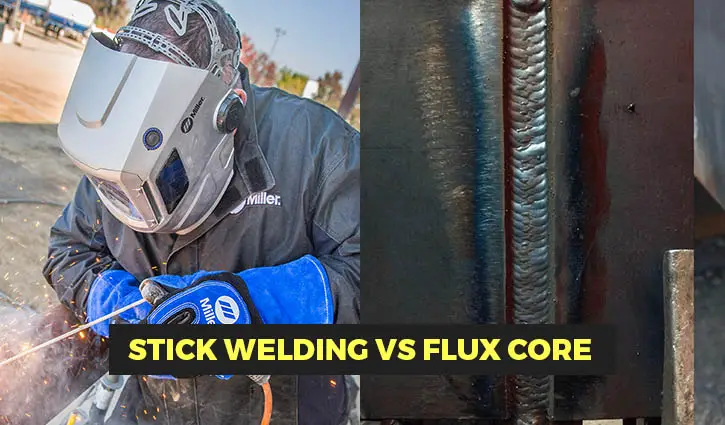
Most individuals find it hard to understand the simple differences between Stick welding and Flux core welding. Well, it is okay to get confused. No worries, the following discussion is for you to clarify the confusion –
Stick Welding Vs Flux Core
Stick welding and flux core welding are affordable and a good suit for the new welders. These are pretty basic techniques for joining metal parts. Each method works in a quite similar way. So, learning the use of one may help to understand the working principle of another.
What Is Stick Welding?
This is the most used welding process among all others. It is well known as SMAW (Shielded Metal Arc Welding). The electrodes used here are inexpensive and good for joining metals with a strong bond.
In stick welding, the metal is inside a flux core. When the stick is connected to the electrode holder and placed closer to the workpiece, the potential differences between the working table and the electrode will generate an arc. Arc generates a huge amount of heat. The rod melts due to the heat and deposits on the joining area.
The flux coating on the outside of the electrode also burns and falls over the molten metal to keep it away from any contamination.
The electrode becomes smaller as the process goes on and the welder needs to adjust the arc distance according to that. Hence the change of electrode is necessary after a certain burn.
What Is Flux Welding?
FCAW or Flux Core Arc Welding follows almost the same process as stick welding, depositing the metals with the heat of the arc.
Flux core welding has a much simpler mechanism and is easily operable for new learners. The wire electrode in the flux core welder needed to be fed by a feeder.
In the flux core electrodes, the flux is covered by the metal surroundings. This mechanism is directly opposite to the electrode of the stick welding.
We know that the electrode in the stick welding shortens as time passes. So, moving the position according to that becomes tough for beginners. Here, the solution lies in the flux core welding mechanism. The device feeds the electrode outward as it shortens. Therefore, the user does not need to change the distance of the arc while welding.
This feature made flux core welding a good suit for new individuals in welding.
The Differences Between Stick Welding And Flux Core
Here are some aspects to look at while differentiating both of the welding procedures. See the table to get a summary of the differences between these two welding processes.
Stick Welding | Flux Core Welding |
The electrode is a Cylindrical Rod type | The electrode is a hollow cylinder type |
Flux positioned at the outer periphery of the rod | Flux is positioned at the inside or the core |
Stick welding employs a shorter length until the change of electrode | Flux core employs more length as the device feeds continuous electrodes |
The equipment used are cheaper and easily operable | Equipment is relatively costly and has a complex set-up |
Deposition of filler metal is low | Deposition of filler metal is relatively high |
The process needed to be carried out manually | The process is semi-automatic or fully in some devices |
The outside flux is prone to grabbing moisture | The flux has none to less chance of catching moisture due to its position inside the metal |
Can weld a wide variety of metals | Suitable for welding the ferrous metals |
Electrode replacement after a certain time hampers productivity | Productivity is better as there is a continuous electrode coming off from the device |
Stick Welding Vs Flux Core Welding: A Detailed Comparison
The basic differences between Stick welding and Flux core welding are in the device type and flux position. And the disadvantages and advantages are followed by these two separate characteristics. Let’s see some more differences between these two-
Price
The device price for stick welding is inexpensive. Also, the filler metals or electrodes are not that pricey. As the procedure involves manual operations, the welding machine is simple, which makes it a cheaper solution.
Flux core welder on the other hand is a complex mechanism. And you need to purchase the whole set to start with flux core welding. This involves a feeder, an automated welder, and the electrodes. So, it is a pricier option for welding.
Usage
Stick welding is used in constructions like shipbuilding, automotive chassis, structural welding, and manufacturing. It can be a wide metal variation.
Flux core welding is suited for joining thicker materials. It ensures a strong and reliable bond. This technique is used for heavy-duty industrial structures. But flux core welding can only be used on ferrous materials.
Strength
Stick welding deposits the filler metal in a low amount. This results in relatively lower strength in the joined portion. The tensile strength in stick welding varies according to the electrode type. This technique can reach up to 70,000.
A good amount of filler metal deposits from flux core welding. Therefore, it results in a good and strong bond between the workpieces. The flux core wire provides a tensile strength of up to 105 KSI, which is relatively very higher than stick welding.
Final Words
Welding can be a bit trickier if you do not understand the procedure. Yet it is the most used metal joining and fabrication procedure among the industries around the globe.
This comparative discussion on Stick welding Vs Flux Core Welding is for giving you a broader view of the differences between the processes.
The beginners should start with flux core welding. Stick welding is much tougher as the individuals need to maintain the ever-decreasing length of the electrode. With a bit of extra price, flux core welding can be the perfect starting point for beginners.